Amazon prides itself on its state-of-the-art fulfillment centers that use innovative technologies and processes to store inventory and quickly ship products to customers. A key component that underpins Amazon’s logistics operations is its License Plate Number (LPN) barcode system for inventory and warehouse management.
Implemented back in 2012, Amazon LPN barcode system assigns unique identification numbers to every pallet that comes into its fulfillment centers. These LPN barcodes allow Amazon to precisely track the quantity, storage location, and status of millions of inventory items in its warehouse network at any given time.
If you sell products on Amazon or are curious how the company leverages technology to enhance its market-leading delivery capabilities, read on to learn more about Amazon’s License Plate Number barcodes. We’ll cover what LPN barcodes are composed of, how they facilitate inventory tracking in Amazon warehouses, and what significant operational benefits they offer a logistics giant like Amazon. Grasping the LPN system provides insight into the sophisticated fulfillment processes that enable Amazon to handle insane order volumes and deliver unmatched convenience for customers.
This overview of the what, why, and how behind Amazon LPN barcodes also highlights why many major retailers are now implementing similar warehouse management systems in their distribution centers.
Unique LPN Barcodes Amazon to Unlock Efficient Warehouse Operations
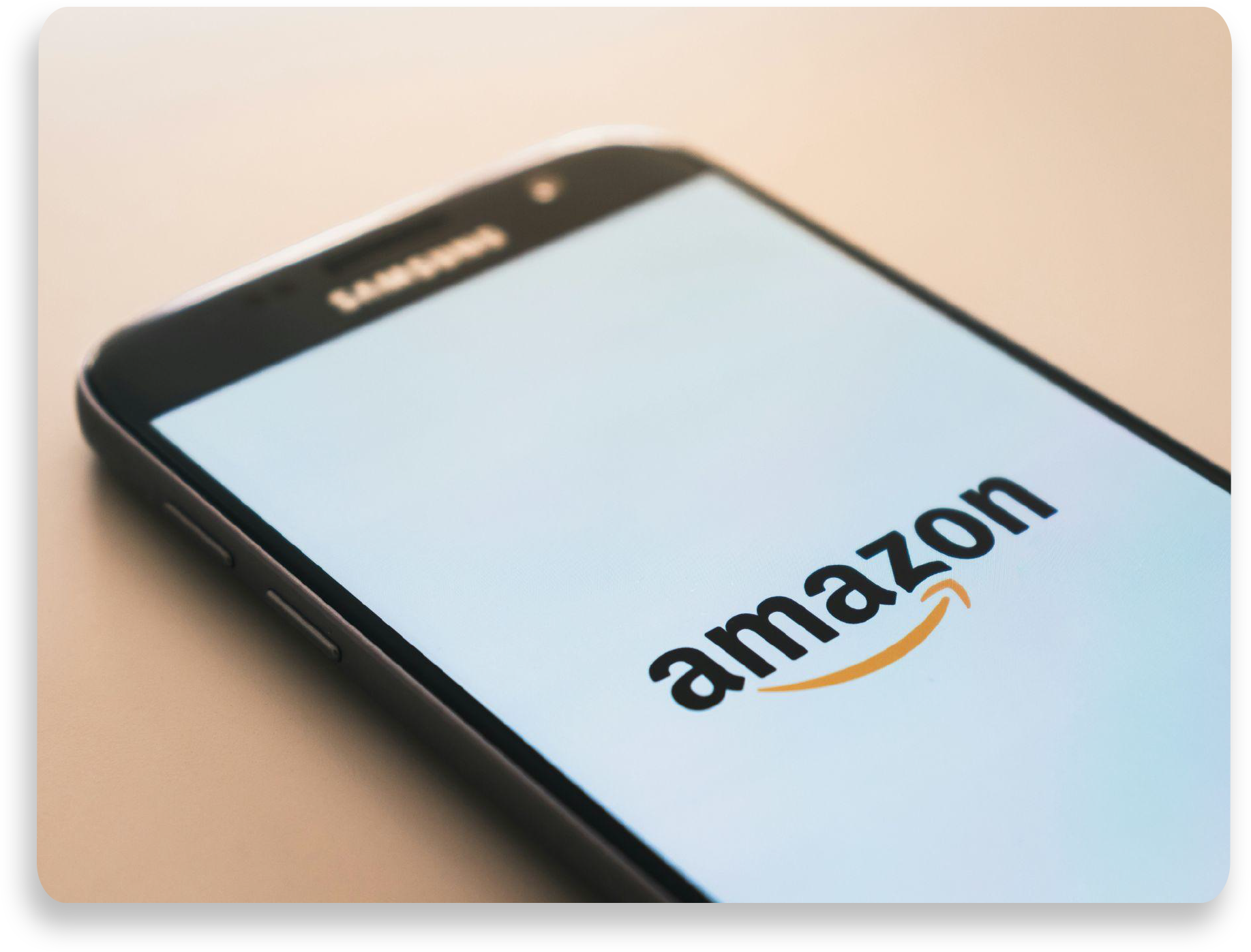
Photo by Christian Wiediger on Unsplash
Amazon utilizes a custom barcode system within its vast fulfillment center network to accurately track the identity, location, and quantity available of millions of products. This proprietary tracking methodology is centered around Amazon License Plate Number barcodes, commonly abbreviated as Amazon LPN barcodes.
When inventory arrives at an Amazon warehouse, unique LPN barcodes are physically applied to every pallet, tote, and other container housing items before they enter storage. This first step of assigning an exclusive identification number is essential for enabling the inventory transparency and operational efficiency gains Amazon’s logistics leaders aimed for when first developing the capability back in 2012 after difficulties managing exponential order growth.
In appearance, an Amazon LPN barcode label resembles a standard one-dimensional barcode containing a 10-digit alphanumeric code. This code transports vital intelligence, allowing Amazon’s scanning systems to rapidly distinguish a specific inventory storage unit from millions of others spread across its fulfillment center empire. The LPN barcode also connects that pallet or container to the precise quantity and type of products contained within.
For example, Pallet A storing 24 boxes of XYZ Brand batteries would get tagged with Barcode LPN: 124A56Z221 upon warehouse receipt. If a robotic drive unit needs to locate and retrieve that exact pallet of batteries to fulfill an order later, scanning the LPN label ensures accurate identification and tracking. Without the unique LPN system in place, reliably finding one pallet among endless rows of tightly packed inventory would prove nearly impossible.
LPN Barcodes Amazon - Vital for Inventory Tracking
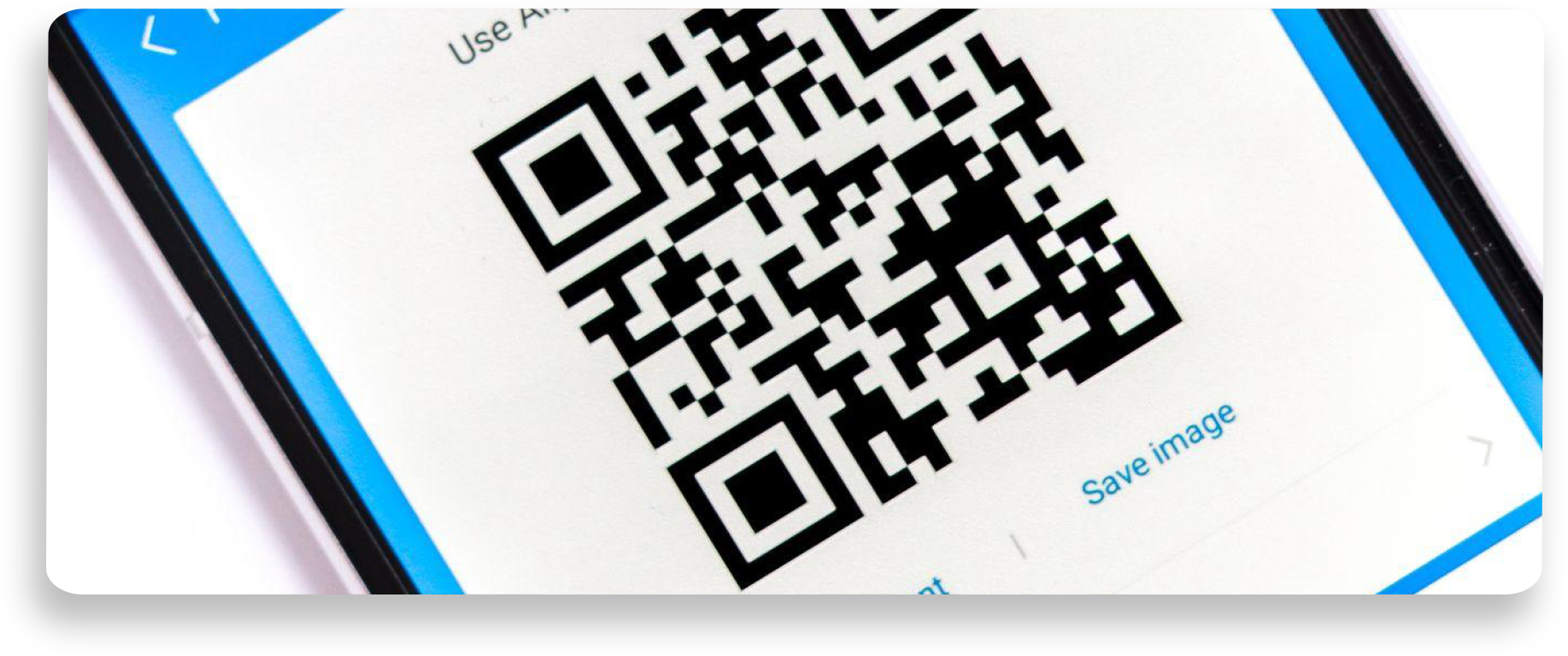
The 10-digit identifiers assigned by Amazon LPN barcode system are more than just random codes. They contain embedded data points that serve an analytical warehouse management software platform underlying Amazon’s logistics operations.
The alphanumeric sequences are constructed using a clearly defined composition that gives the LPN label significant intelligence value when scanned. Let’s break down the typical structure of an Amazon LPN barcode identifier to understand the crucial inventory details encoded:
- First 2 Digits - These numbers identify the specific fulfillment center location out of Amazon’s hundreds of warehouses where the tagged inventory resides.
- Next 2 Digits - Represent the year the inventory/pallet entered the identified fulfillment center. This allows long-term tracking.
- Following 2 Digits - Signify theJulian date showing the actual calendar date when the pallet or tote arrived at the warehouse.
- Final 4 Digits - Form a unique serial number for each license plate barcode printed that day at the fulfillment center.
So an example LPN of “322415189” would break down to:
- 32 - Amazon Fulfillment Center ID
- 24 - Arrived in 2024
- 15 - Arrived on the 15th day of the year (January 15)
- 189 - 189th LPN printed at that warehouse that day
When an Amazon worker or robotic drive unit scans this specific barcode, the warehouse management software gains instant visibility regarding the inventory’s origination details, storage duration, and exact identity. This provides the foundation for the systems making smart routing and storage decisions as other operational processes unfold.
Scanning LPN Barcodes Amazon Enables Real-Time Inventory Tracking
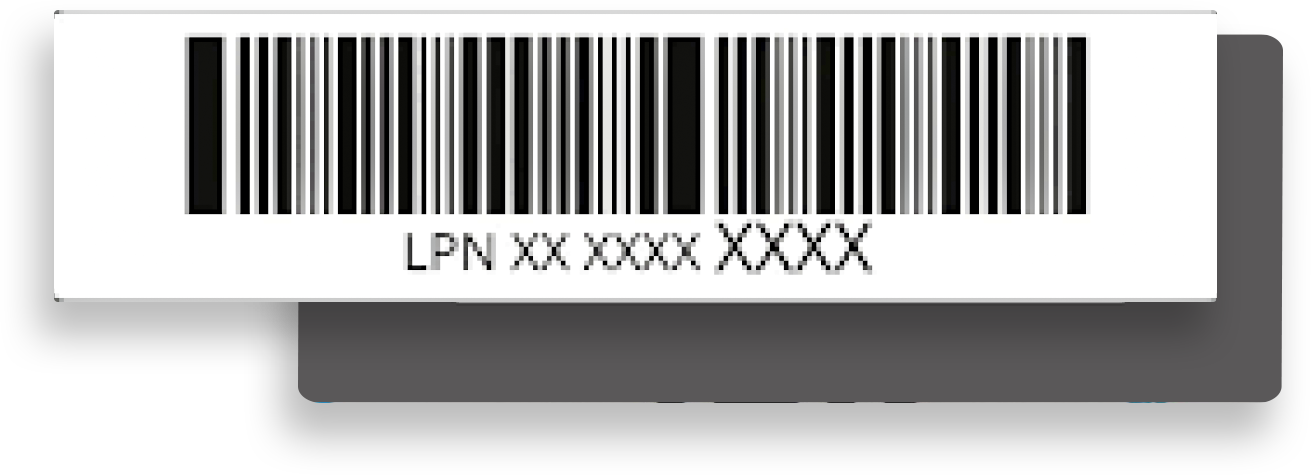
Photo by Markus Winkler on Unsplash
Amazon’s fulfillment centers buzz with activity 24/7. But how does Amazon maintain eyes on inventory as it constantly shifts around warehouses? The answer is relentless scanning of LPN barcodes.
Once LPN barcode labels are applied to pallets and totes, Amazon’s warehouse management software relies on frequent scanning events to track locations and inventory quantities in real-time. When a shipment of products arrives at a loading dock, workers scan the LPN ID tags as containers are unloaded. This checks the inventory into the fulfillment center’s tracking system.
As workers or robotic drive units later retrieve a pallet of items to fulfill orders, the LPN barcode again gets scanned. This may occur multiple times if the inventory gets moved to different interim storage locations before finally reaching a packing station. Each scan updates the tracking record, allowing the warehouse software to monitor how much of a particular product remains.
LPN scans also happen during inbound quality inspections, when restocking pick zones, upon inventory counts, and through all other warehouse workflows. Amazon’s algorithmic systems leverage the constant data intake to optimize subsequent decision-making.
For example, a popular toy with many existing orders may get flagged for priority retrieval over slower-moving inventory when scanning indicates limited remaining quantities. Or an LPN scan might show a particular product overflowing at multiple inbound dock lanes, triggering consolidation into tighter storage arrangements.
Without the abundance of location and quantity data fed through LPN barcode scans, Amazon’s inventory visibility and logistics responsiveness would greatly diminish. But the company’s warehouse management intelligence allows inventory to essentially route itself based on current needs.
Amazon LPN Barcodes Unlock More Efficient Warehouse Operations
It’s easy to recognize the inventory visibility and traceability benefits Amazon LPN barcodes provide. But the increased logistics intelligence also unlocks tangible operational efficiencies across fulfillment centers.
Optimized Storage Utilization & Space Savings By retaining constantly updated data on the types and quantities of inventory stored across all storage zones, Amazon’s warehouse management algorithms can precisely orchestrate daily inventory moves. This allows dynamically maximizing utilization of high-demand storage real estate near active picking stations. At the same time, rarely retrieved long-tail products get efficiently concentrated into deeper storage zones.
Amazon also mixes fast-moving inventory from multiple vendors across LPN-labeled pallets to avoid wasted space. And the company relies on barcode scans to pinpoint partly empty pallets to combine or open new storage slots instead. This optimizationprevents the cost burdens of unnecessarily expanding fulfillment centers.
Lower Labor Costs & Increased Output
LPN barcode scanning also reduces operational expenditures by providing inventory visibility that enables smaller, more productive warehouse teams. Software routes workers and drive units based on current needs instead of exhaustively counting all inventory daily. Scans also validate container contents to avoid employees wasting time double-checking picking instructions.
Along with guiding automation expansion, the rich dataset powered by LPN labels amazon getting scanned allows Amazon to deeply analyze workforce productivity. Software tracks pick rates, route efficiency and other metrics to baseline expectations and performance gaps. This focuses coaching while minimizing micromanagement required.
Fewer Misplaced & Lost Items Mistakes happen, but Amazon LPN barcodes limit the impact of inevitable warehouse inventory mishaps. When an item gets placed on the wrong pallet or shelved incorrectly, LPN scans instantly flag the anomalies so associates can promptly correct issues. This prevents compounding downstream order delays and customer frustrations.
And the system scales across facilities since all Amazon warehouse software shares collective inventory visibility. So products accidentally shipped to the wrong fulfillment center still remain tracked in the system for redirecting. Such resilience and accountability removes significant enterprise risk.
Potential Weak Spots to Understand in Amazon LPN Barcode Tracking
While clearly transformational for Amazon’s logistics operations, the company’s LPN barcode system lacks perfection. Specific vulnerabilities and constraints exist that Amazon sellers and partners should understand.
Fulfillment Center Technology Outages Disrupt Scanning Continuity
Amazon’s warehouse management software and scans rely on perpetual connectivity. Network outages or power failures bring inventory movement and location tracking to a halt. While rare, systems could require heavy reconciliation efforts after coming back online to realign reality.
Careless Associate Scanning Undermines Data Accuracy
Even the most advanced automated systems have vulnerabilities at the human-technology interface. Amazon associates growing weary from repetitive scans or experiencing distraction may mis-scan LPN barcode labels. If the resulting data inaccuracies go unnoticed, downstream processes could unleash chaos.
Limitations Tracking Loose Individual Items
While fantastic tracing standard-sized pallets and totes, LPN barcodes provide no visibility into individual unpackaged items. For products stocked this way, Amazon must rely on more labor-intensive cycle counts for inventory reconciliation. Misplaces remain more likely.
Hardware Failures Impair Barcode Reading Reliability
Laser barcode scanners employ intricate electronic and optical components always at risk of malfunctioning. Dust accumulation, accidental damage drops, and incremental wear will randomly trigger scanner replacement needs. Tech faults could slow warehouse workflows if replacements prove unavailable.
Fulfillment centers represent complex technological and operational ecosystems. So despite undisputed benefits, even advanced systems like Amazon LPN barcode scanners have necessary compromises. But by centralizing inventory data and coordinating human and automated logistics efforts, LPN labels Amazon propel productivity in warehousing’s intricately choreographed dance.
Wrapping Up
Amazon’s License Plate Number (LPN) barcode system has transformed inventory tracing and warehouse management since its rollout. Assigning 10-digit alphanumeric identifiers to every pallet, tote, and container entering Amazon’s fulfillment network unlocked immediate transparency. Now the quantity, locations, and status of millions of products perpetually update through ongoing barcode scans as inventory shifts continuously.
This base-level inventory visibility and real-time movement tracking has proven foundational for automated logistics coordination. Amazon’s warehouse management systems can run optimized storage allocation, picking prioritization, and inventory routing algorithms based on current LPN data. This allows efficiently concentrating fast-moving products near active stations while reducing overlapping restocks. The insights also minimize how much fulfillment center expansion Amazon requires as order volumes grow.
It’s easy to overlook the infrastructure enabling Amazon to handle insane throughput and ship speeds. But the LPN barcode innovation has compressed delivery times from weeks to days to sometimes hours over the company’s rapid expansion. Competitors playing catchup have since implemented similar tracking systems just to remain relevant.
While exploring the inner workings of Amazon’s logistics, sellers and partners better understand the integrating forcing propelling its dominance. But the transparency also reveals dependencies and constraints affecting Amazon’s 2022 holiday peak risks. As more brands rely on its warehouses, all benefit ensuring resilience against disruptions by sustaining optimization focus. Because beyond profits, customer loyalty now centers on fulfillment reliability.
The purpose of Amazon’s License Plate Number (LPN) barcode system is to assign a unique identification number to every pallet, tote, or container that arrives at its fulfillment centers. This system allows Amazon to track inventory location, quantity, and status in real time, ensuring efficient warehouse operations and helping the company fulfill millions of orders quickly and accurately.
An Amazon LPN barcode is a 10-digit alphanumeric code with specific meaning. The first two digits represent the fulfillment center location, the next two digits indicate the year the pallet or tote arrived, the following two digits represent the Julian date showing the exact day of arrival, and the final four digits are a unique serial number printed that day. For example, an LPN code like 322415189 would indicate that the inventory is located in fulfillment center 32, arrived in the year 2024 on the 15th day of the year, and was the 189th LPN printed that day.
Scanning LPN barcodes improves Amazon’s warehouse operations by enabling real-time tracking of inventory as it moves through the fulfillment center. Each time a pallet or tote is received, stored, moved, or picked for orders, the LPN barcode is scanned, updating the system with its new location and status. This continuous flow of data allows Amazon to monitor inventory levels accurately, optimize storage, prioritize picking for high-demand items, and ultimately speed up order fulfillment while reducing errors.
Amazon gains several operational benefits from using LPN barcodes. The system allows for optimized storage utilization by placing fast-moving items closer to picking stations and pushing slower products into deeper storage. It reduces labor costs because workers and robotic systems can rely on the data for efficient routing instead of performing manual counts. It also minimizes mistakes since misplaced or mis-scanned items are quickly flagged and corrected. Overall, the system improves productivity and ensures that inventory moves efficiently throughout the warehouse.
Despite its advantages, the LPN barcode system has some weaknesses. The system is heavily reliant on constant connectivity, so any network or power outage can disrupt scanning and inventory tracking. Human error is another risk, as distracted or fatigued workers may scan incorrectly, leading to data inaccuracies. Additionally, the system struggles to track loose, individual unpackaged items, which still require manual cycle counts. Hardware failures like damaged barcode scanners can also slow operations and create bottlenecks if replacements are not immediately available.